Stahl: 210 GPa
Titan Grade 5: 110 GPa
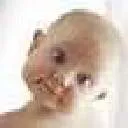
Lightweight Projekt
-
-
Gerade auch noch mal rein geschaut.
Grade 2: 105 kN/mm² und
Grade 5: 114 kN/mm²https://www.thyssenkrupp-materials.ch/de/downloads/w…nblaetter-titan
Also ungefähr die Hälfte.
Lieber diese Rohre als keine. -
Es geht langsam weiter an der Carbon/Kevlar Tür Front.
Konnte letzte Woche und am WE ein wenig weiter bauen. Hab mich jetzt auf alle inneren Teile der Tür vixiert auf die ich eh kein Bock habe, da diese verwinkelt und klein sind. Idee war jetzt alle vier kleinen Winkel und Komponenten zusammen in die Vakuum Tüte zu legen um das ganze mit Vakuum Ziehen, Trocknungszeiten etc. zusammen zu legen. Der Aufbau sah wirklich ganz wild aus. Alle vier Teile waren mit einem Infusionsschlauch zusammengelegt. An der eine oder anderen Stelle musste ich den Schlauch in der Folie verlegen und nachhelfen. Klappte wirklich ganz gut und ich hab an der einen oder anderen Stelle gut dazu lernen können.
Heraus sind dann diese schönen Teile hier.
Um das mal für Euch abbilden zu können. Nur das reine vorbereiten der Carbon / Kevlat Schickten mit der Auslegung der Lagenanzahl, zuschneiden, übereinander legen, Abziehgewebe und Vakuumnetz vorbereiten, aufziehen und verkleben.......jaaaa, gute 7h. Dann das ganze in die Tüte, Vakuum ziehen und Folie und Anformen. Ja und erst dann konnte das Harz angemischt werden und die Infusion gestartet werden.
Nach 24 h Trocknung aus der Form heben, Löcher rein bohren und dieses verdammte Kevlar zeug durchbohren. Das ist an dieser Stelle mal kurz erwähnt eine scheiß ätzende Arbeit die gut Faktor 5-10 dauert. Das Kevlar Gewebe franzt total aus und lässt sich richtig schlecht bearbeiten. Sehr nervig.
Anschließend die Flex angeschmissen und ausgeschnitten. Dann nur noch aus der Form heben und fast fertig. Fast nur deswegen, da sie Aufnahmen für die Seitenaufprallschutz Rohre nicht als Formstück gebaut worden sind. Ich habe diese aus 3 Lagen 205 er Gewebe als Positiv gebaut. Nach abheben aus der Form wird in die neue Innenform abgehoben, dort nun eine entsprechende Anzahl an Carbon/Kevlar Lagen gelegt und dieses Teil neu Infusioniert!
Kann man das verstehen?
Geht darum, dass ich keine separate Form Bauen wollte. Hier sind die Bleche 1,4mm dünn. Da ich alle Bleche mit einem Faktor von 1,5 baue und diese Aufnahmen dann bei ca. 2 mm landen sollen, kann ich an dieser Stelle dies genau so bauen. Wichtig zu erwähnen wäre, dass ich Komponenten die statisch und mechanisch viele Kräfte aufnehmen müssen aus dem Kevlar Hybridgewebe, unterlegt mit dem Carbongewebe baue.
Ein Beispiel?
Hier ist eins.
Der Winkel verstärkt als sehr wichtiges Bauteil die inneren und äusseren Teile Der Tür und dient als ein zentrales Aufnahmestück der Kräfte. Diesen habe ich aus 3x 205 Kevlar und 2 x 600 er Carbon Gewebe gebaut. Das Blech ist ca. 1,4-1,5 mm dick an der Stelle. Wenn ich die Kevlar/Carbon Schichten addiere, sprich....3x205 + 2x600 kommt man auf eine gerechnete Dicke von 1800. Entspricht 1,815 mm + Harzdicke der oberen und unteren Lage......sagen wir mal, dass ich bei dem Stück auf 2,0 mm komme. Und so gestallte ich den Bau aller anderen Komponenten.
An der einen oder anderen Stelle die als Befestigungsstelle für Schrauben dient, lege ich einfach zusätzliche Carbonschickten ein.
So sehen nun die fertigen Teile aus.
Wer sich nun fragt wofür die Löcher dienen......diese sind ja die Punktschweißungen der original Tür. Diese dienen mir nur als exakte Positionierung der Teile für den Zusammenbau.
Und so fügt sich ganz langsam das Puzzle zusammen.
Als nächstes geht es an die Aufnahmen der Rohre.....meine Lieblingsteile....NICHT.
-
Schon geil wie du die Carbonteile daherzauberst
-
Zitat
Frage an UncleHo, warum hast du dieses Teil nicht als ein gemeinsames Teil abgeformt. Zumindest die Enden hätten sich überschneidungsfrei abformen lassen. Auch der Materialmix hätte in einem Durchgang umgesetzt werden können. Liegt das an einer maximalen Größe der Teile (Vakuum) oder ist der Aufwand einfach zu groß?
Wie werden jetzt die Einzelteile zusammengefügt? Genietet oder geklebt?
Meinen größen Respekt vor dieser Arbeit, was du da machst ist extrem.
-
Man bekommt die Teile ja nur separat aus der Tür raus präpariert. Deshalb wird beim späteren Zusammenbau auch so vorgegangen.
-
Wie ihr sehen könnt, ist der Gewichtsunterschied schon nicht zu vernachlässigen. Um nun den Deckel vernünftig bauen zu können, habe ich eine Form gebaut um das Bauteil bezüglich seiner Größe 1:1 nachbauen zu können. Hierzu hab ich einen Abdruck erstellt mit dem ich dann fortfahren konnte. Hier die fertige Form.
Hallo UncleHo
Würde mich interessieren aus was für Material du all die Formen (Abdruck) baust?
Unheimlich mit welcher Passion du dahinter bist!
-
Hierzu gibt es spezielle 2k Abformpasten in die ein Härter gemischt wird und man dann einen Formenbau macht. Musst mal einige Seiten zurück gucken als ich den Tankdeckel mit genau dieser Abformpaste gebaut habe.
Und danke für die Blumen. Macht ja auch Spaß.
-
Alter Schwede, wenn ich mir nur vorstelle wieviel Stunden und Geduld da reingehen.
Von den Materialkosten gar nicht zu reden.
Respekt Chris!
-
Echt beeindruckend 👍 Dieses Auto wirst du mit Sicherheit nie verkaufen.
-
He he...vielen Dank Euch.....
Also verkaufen will ich den nicht, neeee
Stunden mäßig hab ich jetzt mal pro Tür mit 300 h geplant. Bin jetzt bei ca. 50 h. Somit ist noch einiges offen......alles nach und nach und irgend wann wird sie fertig sein.
Habe mir so April/Mai als Ziel gesetzt..
Hier der aktuelle Stand der Tür.
Dellen sind nun alle gespottert worden, die Aufnahme der Spiegel kommt nun auch weg. Da hab ich mir was neues überlegt. Die neuen kommen an die Dreiecksstücke der Tür.
Und hier noch mein Kunstwerk der vier Teile in einem Vakuumbeutel.
Bis dann,.....morgen wird weiter gebaut.
UncleHo
-
-
die Aufnahme der Spiegel kommt nun auch weg. Da hab ich mir was neues überlegt. Die neuen kommen an die Dreiecksstücke der Tür.
Na endlich geht mal jemand das Thema Dumbo-Ohren an.
-
Hallo zusammen,
kleines update zur Lage der Nation
Der Patient lebt noch und Uncle hat nun endlich die erste der vier Seitenaufplall Schutzeinrichtung fertig. Eine richtig kack Arbeit.
Zum Teil dauerte es 2 h um das Abreißgewebe vom Halter zu kratzen. Wie immer entschädigt das Ergebnis unheimlich und die Gewichtsersparnis kann sich sehen lassen.
Des Weiteren konnte ich weitere innenliegende Teile der rechten Tür bauen. Hierzu gehört der Schlossträger der Führungsschiene. Hier habe ich lange überlegt, ob ich denn dieses Teil überhaupt in Carbon baue oder nicht. Habs dann doch gemacht
Jedes Gramm zählt und wenn man schon mal dabei ist kommt es auf die 5 h auch nicht mehr an.
Also das original teil wiegt 31g inklusive der Gewindeaufnahmen. Diese habe ich übrigens mit Feinwerkzeug rauspräpariert um diese weiterhin nutzen zu können.
und
Die Hauptaufnahmen des Seitenaufprallschutzes waren die absoluten Knackpunkte. Aber auch das konnte erfolgreich erledigt werden.
Dies ist die vordere Aufnahme. Ebenfalls auch hier habe ich die Gewindeaufnahmen aus dem Original ausgebohrt um diese hier verwenden zu können. Das original Teil wiegt 129 g. Die Hintere Aufnahme wird mit einem zusätzlichen Blech am Rahmen der Tür geklemmt. Diese platte habe ich ebenfalls nachgebaut. Diese wiegt 48 g als original.
Meine nun
und zu guter letzt kommt die hintere Aufnahme. Diese hat mich sehr viel Zeit gekostet. Ebenfalls wie bei der vorderen Aufnahme habe ich diese aus Aramid Carbon Hybridgewebe gebaut. Als Faktor habe ich das 1,5 fache angepeilt. Somit sind diese Bauteile bei ca. 2,0 mm Dicke gelandet. Um auch die statische Festigkeit im Falle eines Aufpralles abbilden zu können habe ich die Bauteile aus 5 x Aramidgewebe 205 g/cm² und 1 x 600 g/cm² Carbongewebe gebaut. Sollte nun genug Sicherheit in der Konstruktion stecken.
Das original wiegt 160 g
Und morgen zeige ich Euch ein weiteres Tuningteil, dass um die 4000 g Ersparnis bringen wird.
Danke schon mal an Berz für deine Hilfe.
-
Bin fassungslos mit welcher Hingabe Du da unterwegs bist
Nach einem Jahr überwiegend Homeoffice sollte ich mal mein persönliches Lightweight Projekt starten
Geht da was mit Carbon
-
Nach einem Jahr überwiegend Homeoffice sollte ich mal mein persönliches Lightweight Projekt starten
Geht da was mit Carbon
Oh, diese leidliche Erfahung teile ich auch und schließe ich mich mal an. Da liegt bei mir auch noch 'ne Menge Lightweight-Potential. Wobei ich keine Carbon-Wampe haben möchte ... die kann einfach nur weg.
Berz hat doch nicht etwa ein "Carbon-superleicht-Öl" entwickelt, das perfekte Schmiereigenschaften hat und weniger als die Hälfte als das Reguläre wiegt, oder?
-
Berz hat doch nicht etwa ein "Carbon-superleicht-Öl" entwickelt, das perfekte Schmiereigenschaften hat und weniger als die Hälfte als das Reguläre wiegt, oder?
Ne, ich habe ihm eine Feststoffschmierung verpasst, all das nervige flüssige Zeug raus und wir müssen auch nicht mehr darüber diskutieren. Und es spart natürlich Gewicht 💪🏼 🥸🤌🏼
-
So, wie angekündigt.....
mal was anderes als immer der Carbon Scheiß
Onkel Berz war mal wieder für mich tätig und hat gutes getan
Kleiner Einkauf in Japan war fällig. Ich konnte den -4 kg einfach nicht widerstehen. Und dann auch noch rotierende Masse
Und hier ist Sie....
Habe jetzt leider nicht gucken können was Toda für die separaten Gewichte angibt. Wichtig war an dieser Stelle einfach mal festzustellen wieviel die separaten Komponenten wiegen.
Druckscheibe: 4550 g
Kupplung: 1219 g
Schwungscheibe: 4957 g
In Summe und mit einer anderen Waage kommen die 10880 g zusammen. Wenn man die anderen Gewichte addiert kommt man auf 10726 g. Leider habe ich vergessen die 6 x M8 oder warens doch M10 er Schrauben zu wiegen. Denke mal, dass die Differenz aber gut hinkommt.
Also Berz, danke noch mal!!!
Einbau folgt im Mai bei Sonnenschein, Bier und Grill ganz entspannt an der Halle
Grüße Uncle
-
Konnte gestern meine alten Kupplungskomponenten wiegen-
Kupplung OEM: 1330 g
Druckplatte OEM: 4656 g
Ne Schwungscheibe hatte ich jetzt leide nicht zur Hand.
-
Schwungscheibe am AP1 hat etwas über 6 kg. 6,1 oder 6,3 Kg... Könnte meine alte mal wiegen, wenn du magst.
-